categorieën: Hoe werkt het
Aantal keer bekeken: 23713
Reacties op het artikel: 1
Hoe de plasma-lasmachine is opgesteld en werkt
Plasma in de fysica is de vierde toestand van materie na vaste, vloeibare en gasvormige vormen, wanneer gedeeltelijke of volledige ionisatie van het medium uit eerder neutrale moleculen en atomen plaatsvindt, afhankelijk van de quasineutraliteit: de volumedichtheid van alle geladen deeltjes is gelijk.
In de lastechnologie worden de volgende eigenschappen van plasma bij lage temperatuur (minder dan een miljoen graden Kelvin) gebruikt:
-
zeer hoge elektrische geleidbaarheid;
-
de sterke invloed van externe magnetische velden op de stroom van stroom, die bijdraagt aan de vorming van stralen en lagen;
-
manifestatie van collectieve effecten, uitgedrukt door de overheersing van magnetische en elektrische krachten boven zwaartekracht.
Principes voor het maken en bedienen van plasmatoortsen
Bij deze lasmethode is de bron van het verwarmen van metalen tot het smeltpunt een plasmaboog van geïoniseerd gas, die in de juiste richting wordt gericht. Het wordt geproduceerd door een speciaal apparaat dat een plasmatron of plasmatoorts wordt genoemd.
Indeling naar type boog
Door het werkingsprincipe kan de plasmatron van directe of indirecte actie zijn.
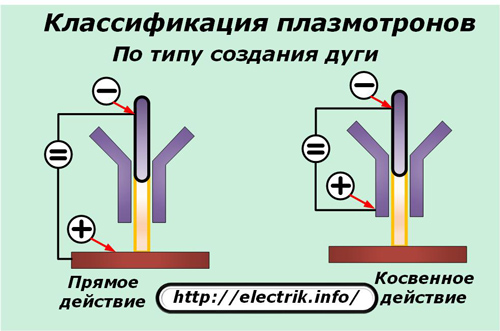
In het eerste geval wordt het potentiaalverschil van het externe veld van de generator, waardoor de voorwaarden voor de vorming van een boog worden gecreëerd, rechtstreeks op het werkstuk en de elektrode van de gasbrander toegepast. Hierdoor wordt de koelefficiëntie van de structuur verhoogd.
In de tweede methode wordt elektrische spanning alleen tussen de delen van de brander aangelegd om een plasmastraal te creëren. Vanwege dit is het noodzakelijk om het koelsysteem van het mondstuksamenstel ingewikkeld te maken.
Voor direct werkende plasmatrons wordt een boog geproduceerd die ongeveer lijkt op een cilindrische vorm, die enigszins uitzet aan het oppervlak van het metaal dat wordt verwerkt.
In het neutrale elektrische mondstuk vindt compressie en stabilisatie van de boog plaats. In dit geval vormt de combinatie van de thermische en kinetische energie van het plasma er een groter vermogen voor, waardoor het metaal dieper smelt.
Indirecte branders creëren een plasma in de vorm van een conische straal omringd door een toorts die naar het product is gericht. De straal wordt uitgeblazen door de plasmastroom die uit de brander komt.

Classificatie van branderkoelmethoden
Vanwege de hoge temperatuur van het plasma worden verschillende methoden voor het koelen van de details van de plasmatoorts gebruikt:
-
lucht blazen;
-
warmteafvoer door geforceerde watercirculatie.
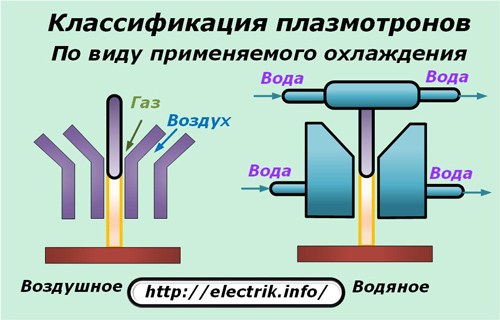
Luchtkoeling is goedkoper en vloeistofkoeling is het meest efficiënt, maar complex.
Classificatie van boogstabilisatiemethoden
De gasbrander moet een gelijkmatige, stabiele grootte en richting temperatuurkolom bieden met een strikte fixatie ervan langs de as van het mondstuk en de elektrode.
Daartoe zijn drie soorten spuitdopontwerpen met energie ontwikkeld:
1. gas;
2. water;
3. magnetisch veld.
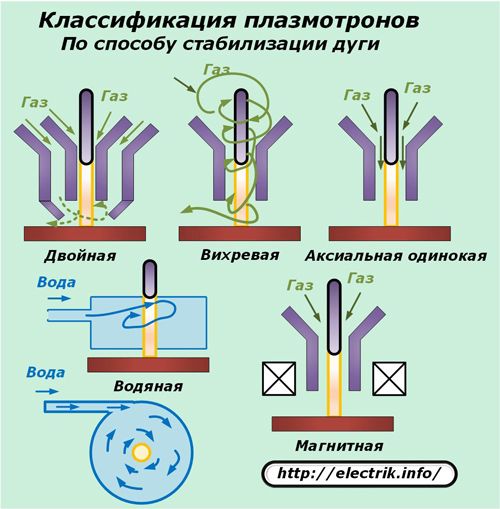
In de eerste methode een koude gasstroom die een kolom met plasma blaast, koelt en comprimeert deze tegelijkertijd. Afhankelijk van de richting van de gasstroom wordt stabilisatie gecreëerd:
1. axiaal - met parallel blazen van de kolom;
2. wervelen wanneer de gasstroom in de loodrechte richting wordt gecreëerd.
De tweede methode comprimeert de boog efficiënter en wordt gebruikt in plasmatrons die worden gebruikt voor metaalafzetting of snijden.
Axiale stabilisatie is beter geschikt voor het lassen en oplassen van metalen.
Het dubbele stabilisatieschema combineert de kenmerken van axiaal en vortex. Bij gebruik is het mogelijk om op drie manieren gas door te geven:
-
alleen via het centrale hoofdkanaal;
-
door beide;
-
uitsluitend via extern.
Elke methode creëert verschillende schema's voor het comprimeren van de plasmakolom.
Waterstabilisatie gebruikt tegenwervelende vloeistofstromen.De stoom die in dit proces wordt gegenereerd, helpt om plasma te maken met een kolom die tot 50 duizend graden op de Kelvin-schaal wordt verwarmd.
Een belangrijk nadeel van deze methode is de intense verbranding van de kathode. Voor dergelijke apparaten is de elektrode gemaakt van grafiet, waardoor mechanismen worden ontwikkeld voor de automatische benadering van het werkstuk naarmate de lengte continu wordt verbruikt.
Water-gestabiliseerde plasmatoortsapparaten worden genoteerd:
-
ontwerpcomplexiteit;
-
lage betrouwbaarheid van het elektrodetoevoersysteem;
-
de complexiteit van de excitatiemethoden van de boog.
Magnetische stabilisatie Het werkt vanwege het directionele magnetische veld dat zich over de beweging van de boogkolom bevindt. Het rendement is het laagst, en de in de spuitmond ingebouwde solenoïde bemoeilijkt het plasmatoortscircuit aanzienlijk.
Magnetische stabilisatie wordt echter gebruikt om rotatiebeweging aan de anodevlek binnen de wanden van het mondstuk te geven. Dit maakt het mogelijk om de erosie van het mondstukmateriaal te verminderen, wat de zuiverheid van de plasmastraal beïnvloedt.
Alle constructies van plasmatrons die hierboven zijn overwogen, zijn boogvormige. Maar er is een ander soort soortgelijke plasma-genererende apparaten vanwege de energie van de hoogfrequente stroom die door de inductiespoel stroomt. Dergelijke plasmatrons worden inductie (HF) genoemd en vereisen geen elektroden om een boogontlading te creëren.
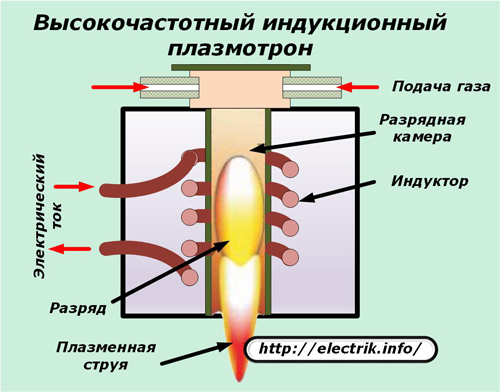
Ze hebben geen speciale voordelen bij het beïnvloeden van de bewerkte metalen in vergelijking met boogapparaten en worden gebruikt om individuele technologische processen op te lossen, bijvoorbeeld de productie van pure poedermetalen.
Ontwerpkenmerken van branders
De werking van een van de soorten plasmatoortsen kan worden verklaard door de onderstaande figuur.
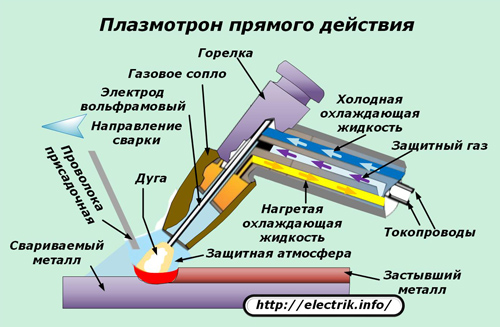
De plasmaboog tijdens het lassen wordt gecreëerd in de beschermende atmosferische schaal gevormd door het toevoeren van geïnjecteerd gas naar het werkgebied. Ze kiezen meestal argon.
Plasmavormend gas (ionisatiebron) kan werken:
-
argon;
-
stikstof;
-
helium;
-
lucht;
-
waterstof;
-
mengsels van de genoemde gassen.
Houd rekening met de kenmerken van hun werking:
-
waterstof is explosief;
-
nitriden en ozon komen vrij uit de lucht;
-
helium schat;
-
Stikstof bij hoge temperaturen beïnvloedt het milieu.
Wolfraam wordt meestal gekozen als het materiaal voor de elektroden vanwege de meest geschikte mechanische eigenschappen en weerstand tegen hoge temperaturen.
Het gasmondstuk is vast in de brander en wordt geblazen met een beschermende stroom. Koude vloeistof wordt langs de hydraulische leidingen gepompt en verwarmd wordt afgevoerd.
Stroomvoerende draden leveren elektrische energie van gelijkstroom of wisselstroom aan de elektroden.
Om de plasmavormende boog van stroom te voorzien, is een stroombron met een spanning van ongeveer 120 volt aangesloten voor lassen en ongeveer 300 in rust - voor snijden.
Apparaat voor plasmagenerator
Wisselstroom of gelijkstroom kan worden gebruikt om de plasmatron te starten. Overweeg als voorbeeld de werking van een generator van conventioneel voedingsnetwerk 220 volt.
Ballastweerstand beperkt voedingsstroom. De gashendel regelt de belasting. De diodebrug converteert een wisselspanning om een werkingsboog te handhaven.
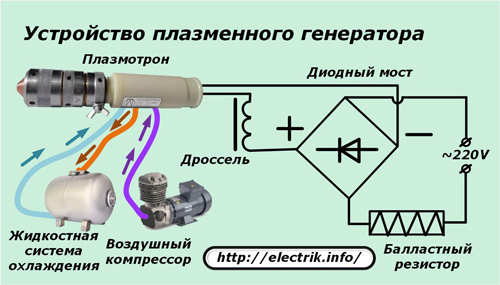
Een luchtcompressor levert beschermgas aan de brander en een hydraulisch koelsysteem circuleert de vloeistof in de plasmalijnen om effectieve warmteafvoer te handhaven.
Techniek voor plasmalassen en -snijden
Voor ontsteking en onderhoud van de lasboog wordt elektrische stroomenergie gebruikt en voor de contactloze excitatie een oscillator (oscillatiebron).
Het gebruik van een pilootboog tussen de elektrode en het mondstuk kan het starten van het plasma aanzienlijk vergemakkelijken.
Met dergelijk lassen kunnen bijna alle metalen en legeringen in het onderste of verticale vlak worden verbonden.
Zonder de randen voor te bewerken, kunnen schuine kanten met een dikte tot 15 mm aan schuine kanten worden gelast.In dit geval wordt een karakteristieke penetratie met specifieke vormen gevormd als gevolg van de uitgang van de plasmastraal voorbij de achterkant van het gelaste deel door de doorgaande gleuven.
Plasmalassen is in de meeste gevallen zelfs een dubbel continu proces:
-
doorsnijden van het werkstukmateriaal;
-
lasplaats gesneden.
Snijtechnologie is gebaseerd op:
-
gesmolten metaallaag op de behandelingsplaats;
-
blazen van de vloeibare fractie in de plasmastroom.
De dikte van het metaal beïnvloedt de snijtechnologie. Voor dunne producten wordt de indirecte methode gebruikt en voor dikkere producten werken direct aangesloten plasmatoortsen beter.
Plasmasnijden is het meest economisch voor alle metalen, inclusief koolstofstaal.
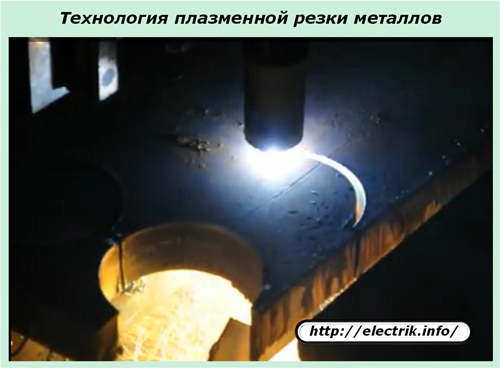
Om plasmalassen en -snijden uit te voeren, zijn geautomatiseerde lijnen en handmatige installaties ontwikkeld.
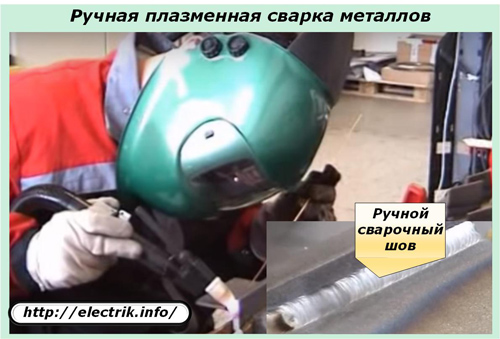
Soorten plasma-lassen
De kracht van de toegepaste stroom beïnvloedt de kracht van de gecreëerde boog. Drie soorten lassen worden bepaald door de grootte:
1. microplasma;
2. gemiddeld;
3. bij hoge stromingen.
Microplasma lassen
Het werkt op stromen beperkt tot 0,1 ÷ 25 ampère. Deze technologie wordt gebruikt in elektronica, instrumentatie, sieraden, productiebalgen, membranen, thermokoppels, folie, dunwandige buizen en containers, zodat u onderdelen met een dikte van 0,2 ÷ 5 mm stevig kunt verbinden.
Om verschillende materialen te verwerken, worden combinaties van plasmavormende en beschermende gassen, de compressiegraad van de boog en de nabijheid van de anode gekozen. Bij het verwerken van in het bijzonder dunne materialen, wordt de pulsmodus gebruikt voor laagspanningsvoeding van de boog met de toevoer van bipolaire stroompulsen.
Tijdens het passeren van een puls met één polariteit wordt metaal afgezet of gelast en wanneer het wordt gepauzeerd vanwege een verandering in richting, koelt het metaal af en kristalliseert het, en wordt een laspunt gecreëerd. Voor zijn goede opleiding is het proces van stroomtoevoer en pauze geoptimaliseerd. In combinatie met amplitudecontrole en elektrodeverwijdering, maakt dit het mogelijk om hoogwaardige verbindingen van verschillende metalen en legeringen te bereiken.
Om microplasma-lassen uit te voeren, zijn veel technologieën ontwikkeld die rekening houden met verschillende hellingshoeken van de plasmatoortsen, waardoor transversale trillingen voor de vernietiging van oxidelagen ontstaan, het mondstuk wordt verplaatst ten opzichte van de las die wordt verwerkt, en andere methoden.
Plasmalassen bij gemiddelde stromen van 50 ÷ 150 ampère gebruikt in industriële productie, machinebouw en reparatiedoeleinden.
Hoge stromingen vanaf 150 ampère worden gebruikt voor plasmalassen die industrieel gelegeerd en koolstofarm staal, legeringen van koper, titanium, aluminium verwerken. Hiermee kunt u de kosten van snijkanten verlagen, de productiviteit van het proces verhogen en de kwaliteit van de naden optimaliseren in vergelijking met elektrische boogmethoden.
Plasma metaaloppervlakken en oppervlaktespuiten
Afzonderlijke machineonderdelen vereisen de levering van hoge sterkte of bestand tegen oppervlakken met hoge temperaturen of agressieve omgevingen. Daartoe worden ze bekleed met een beschermende laag van duur metaal door plasmabehandelingsmethoden. Hiervoor wordt de voorbereide draad of poeder in fijne korrels in de plasmastroom gebracht en in gesmolten toestand op het te behandelen oppervlak gesproeid.
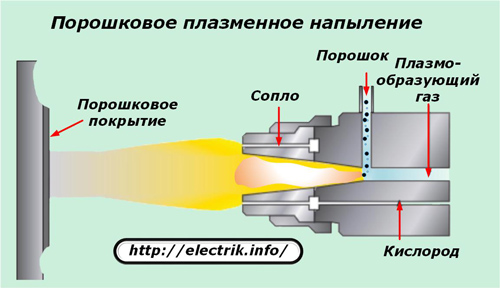
Voordelen van deze methode:
-
het vermogen van plasma om metalen te smelten;
-
het vermogen om legeringen van verschillende samenstellingen te verkrijgen en meerlagige coatings te creëren;
-
de beschikbaarheid van verwerkingsformulieren van elke grootte;
-
gemak van aanpassing van de energiekenmerken van processen.
Voordelen van plasmalassen
De boogbron gecreëerd door plasma-lassen verschilt van conventionele elektrische:
1. een kleiner contactgebied op het behandelde metaal;
2. groter thermisch effect door de benadering van een cilindrische vorm;
3. verhoogde mechanische druk van de straal op het metaal (ongeveer 6 - 10 keer);
4. Het vermogen om boogbranding bij lage stromen te handhaven, tot 0,2 ampère.
Om deze vier redenen wordt plasma-lassen beschouwd als veelbelovend en veelzijdig in metaalverwerking. Het zorgt voor beter smelten binnen een verlaagd volume.
De plasmaboog heeft de hoogste temperatuurconcentratie en stelt u in staat metalen met een grotere dikte te snijden en te lassen, zelfs met bepaalde toenamen in de afstand van het brandermondstuk tot het werkstuk.
Bovendien verschillen plasma-lasapparaten:
-
relatief kleine afmetingen;
-
betrouwbaarheid op het werk;
-
eenvoud van stroomregeling;
-
gemakkelijke start;
-
snelle beëindiging van de bedrijfsmodus.
tekortkomingen
De hoge kosten van apparatuur beperken de wijdverbreide introductie van plasma-lassen in alle industrieën en bij kleine ondernemingen.
Zie ook op electro-nl.tomathouse.com
: